In 2022, we shared our vision for transforming plastics through an innovative collaboration with the U.S. Department of Energy's BOTTLE Consortium. Today, that vision is advancing from laboratory concept to commercial trials. Through work with our partners — from material scientists to recycling facilities to Amazon Fresh stores — we're demonstrating the steps to prove out a new value chain for plastics that are derived from renewable resources and easily recyclable, while also being naturally biodegradable.
When we first started this work, we knew we needed to develop a new recycling technology that could efficiently process biodegradable plastics, as that is not something that exists at scale today. Our specific focus was on polyester-based biodegradable plastics. The molecular backbones of these plastics contain carbon-oxygen ester linkages, which are much easier to break down than the carbon-carbon bonds found in more common plastics, such as polyethylene or polypropylene.
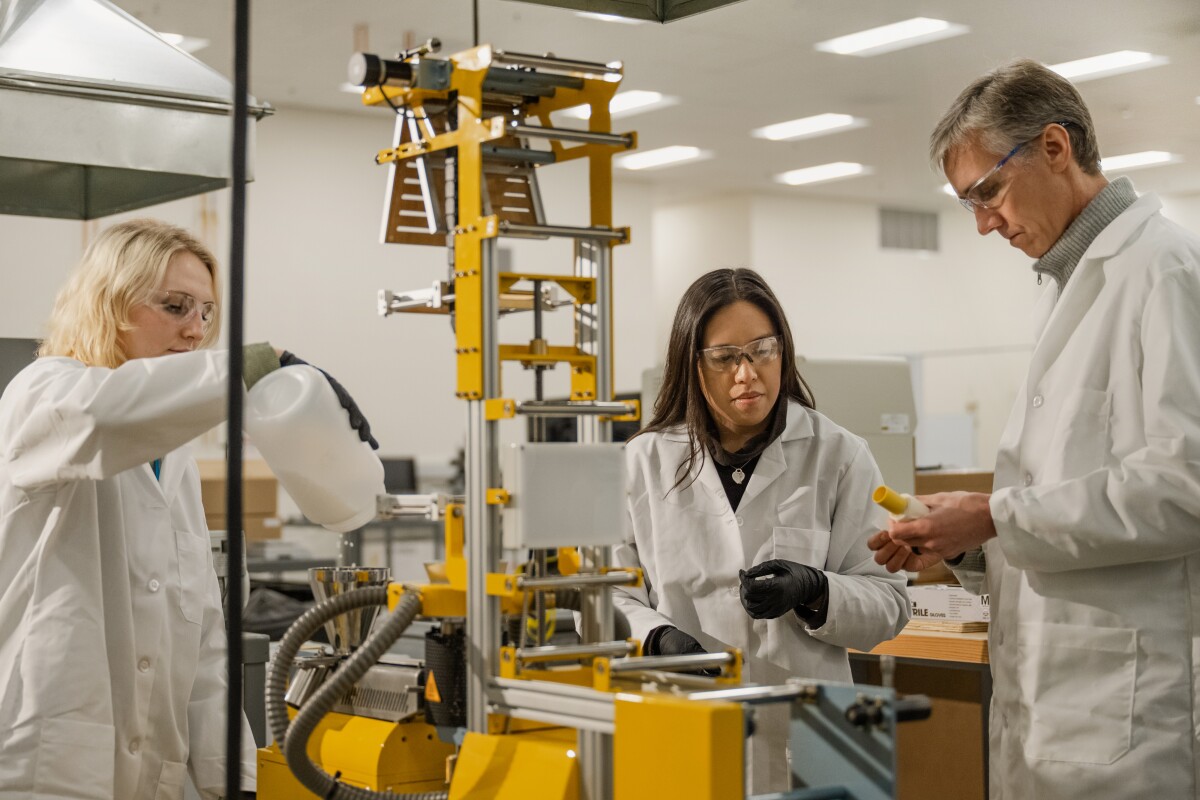
The ester linkages that make these types of plastics more susceptible to biodegradation also make them easier to break down in controlled environments where the remaining molecules can be recycled back into new materials. Solvolysis techniques, such as methanolysis and glycolysis, are being developed for polyethylene terephthalate (PET), but they could be extended to other polyesters, such as polylactic acid (PLA) or polyhydroxyalkanoates (PHAs), that are more readily biodegradable.
While focusing on recycling polyester-based biodegradable plastics — or biopolyesters, for short — we also aimed to make this new recycling technology work for a mixed-waste stream of materials. There is no single biodegradable plastic that can meet the diverse needs of different packaging applications, and applications will often require blends or different materials layered together.
Having a separate recycling stream for each new type of biopolyester plastic would be impractical and likely uneconomical. It also would not solve the problem of recycling blends and multilayered materials. Working backward from this insight, we partnered with scientists at the National Renewable-Energy Laboratory (NREL) to conduct a comprehensive analysis comparing different chemical recycling approaches for recycling a mixed-waste stream of polyester-based plastics.
Our initial analysis, which was recently published in One Earth, provided the scientific foundation for what would become EsterCycle™, a new startup founded by one of our collaborators at NREL, Julia Curley. EsterCycle™’s technology uses low-energy methanolysis processes with an amine catalyst to selectively break the ester bonds that hold these polymers together.
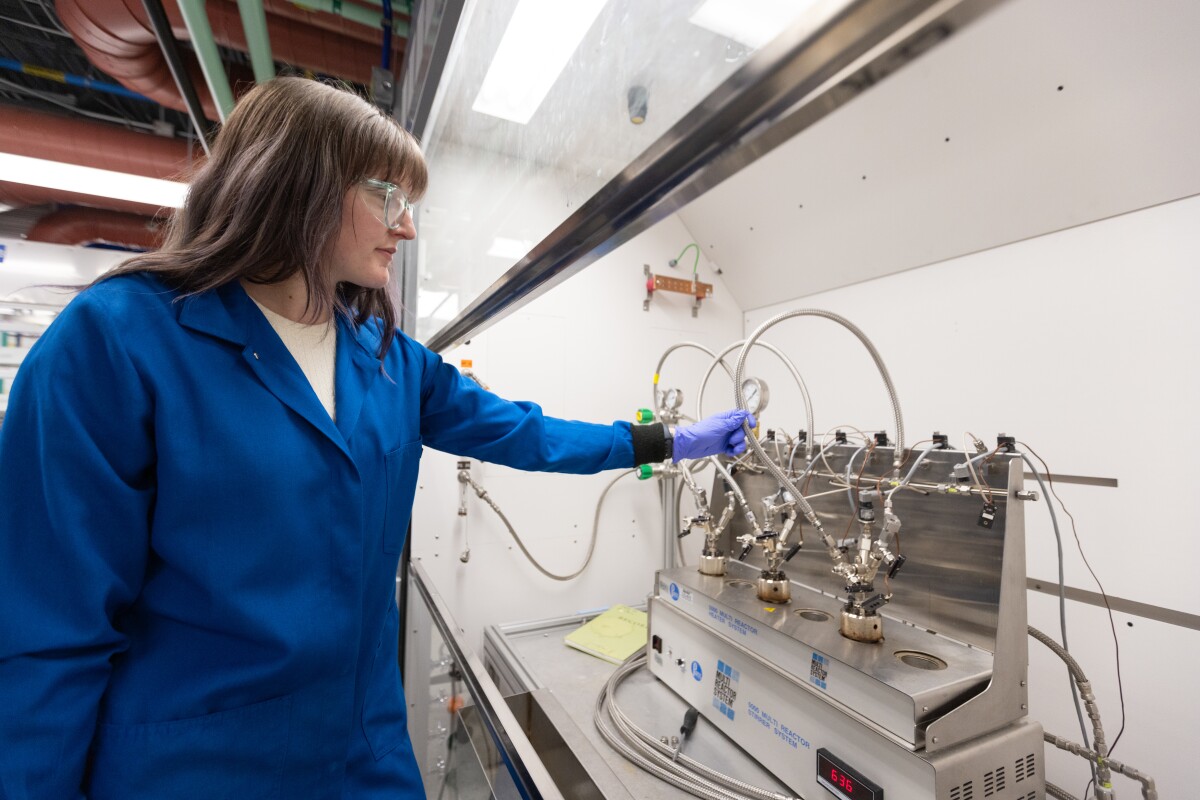
Importantly, the recycling technology was developed to handle a mixed-waste stream of polyesters without requiring extensive sorting of different materials beforehand. This is a crucial advantage because it means we can start recycling biopolyesters even while they represent a small portion of the waste stream, processing them alongside more common materials like PET.
The development of the EsterCycle™ technology represents a key step toward our vision of a more sustainable circular value chain for plastics, but for EsterCycle™ to succeed at scale, there needs to be a reliable supply of materials to recycle. This is where our partnership with Glacier Technologies comes in.
Glacier, which Amazon’s Climate Pledge Fund recently invested in, uses AI-powered robots to automate the sorting of recyclables and collect real-time data on recycling streams. In real time, Glacier’s proprietary AI model can identify a range of different material and package types, from rigid PET containers, such as thermoformed clam shells, to multi-material flexible packaging, such as snack bags.
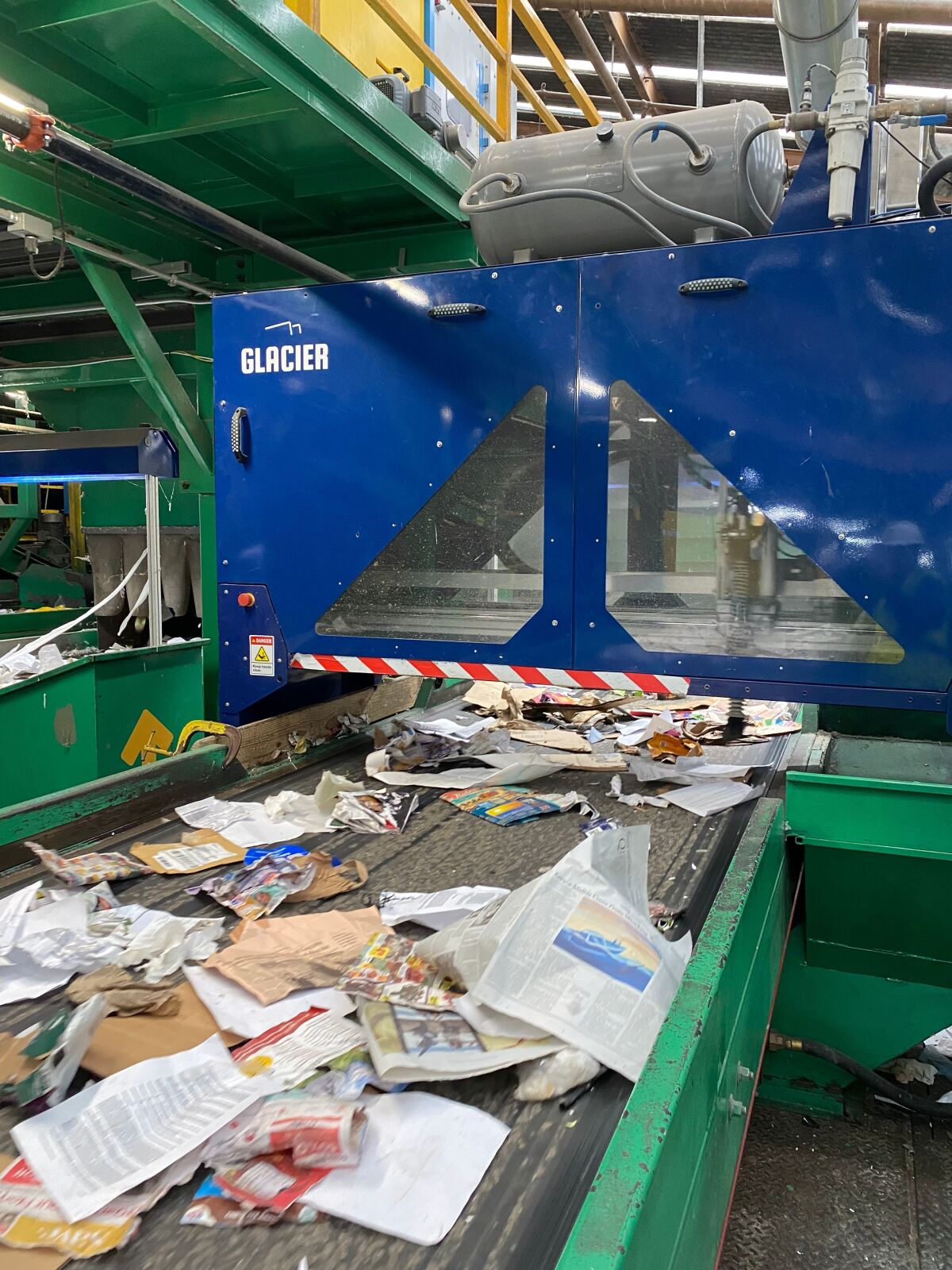
We launched a sortation trial with Glacier and a recycling facility in San Francisco to test how effectively Glacier’s AI vision and robotic systems could identify and sort biopolyester packaging. A key insight from these trials was that packaging design significantly influences AI detection. Packaging with consistent, visible features was identified correctly by Glacier's AI models 99% of the time. However, lookalike materials and inconsistent designs led to higher rates of misidentification. These results will help us and our partners design packaging that's easier to recycle as we design and test emerging biopolyesters for new applications.
Our next step in helping build out this new value chain for plastics was to test and trial emerging biopolyesters in real-world applications. Our first priority is to minimize packaging — and even eliminate it, where possible. But there are some applications where packaging is necessary, and paper is not a viable option — particularly, applications with specific and stringent requirements, such as moisture barrier properties. To understand how biopolyesters perform in these critical applications, we launched several commercial trials across our operations.
In Seattle, we tested biopolyester produce bags made with Novamont's Mater-Bi material in Amazon Fresh stores. Customer feedback was overwhelmingly positive, with 83% of Amazon Fresh customers reporting they "really liked" the new compostable bags. Our shelf-life testing showed that the bags performed similarly to conventional plastic bags in keeping produce fresh for the first week after purchase, though different types of produce showed varying results in longer-term storage, which is an area where we are working with materials developers to improve.
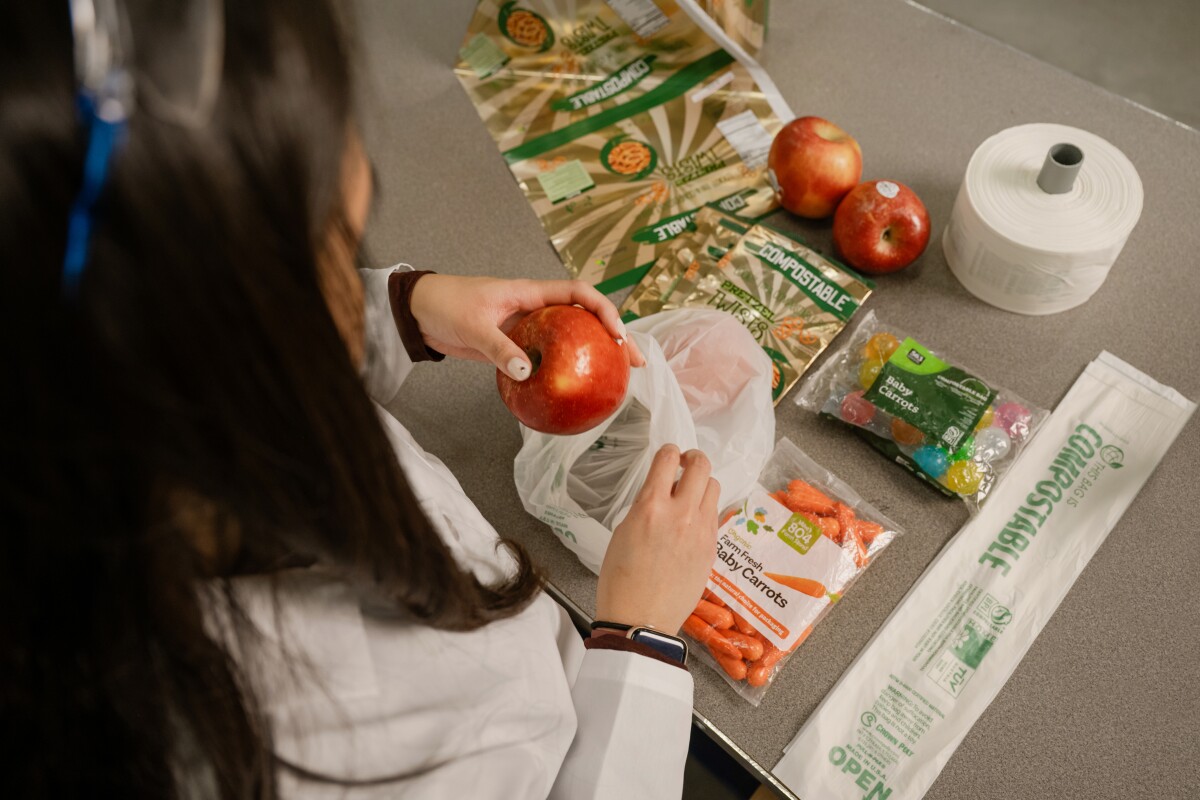
In Europe, we successfully trialed biopolyester prep bags at three Amazon fulfillment centers near Milan, Italy. The majority of associates reported that the biopolyester bags were just as easy to use as conventional plastic bags, with no impact on operational efficiency. Similarly, in Valencia, Spain, we tested biopolyester bags for grocery delivery through Amazon Fresh. This trial actually showed improvements in quality metrics, including reduced rates of damaged and missing items compared to conventional packaging.
These trials demonstrate that biopolyester materials can effectively replace conventional plastics in many applications while delighting customers and enabling continued operational excellence. The data and findings from these trials are helping build confidence across the industry around these new materials, which is crucial for driving broader adoption to replace conventional plastics.
Today, we cannot yet recycle these materials at scale, so composting is the interim end-of-life option. However, as EsterCycle scales, and as Glacier enables more materials recovery facilities to sort a range of different polyesters, from PET to PLA to new PHAs, we envision a future where these materials are widely accepted in household recycling programs, making it easy for our customers to recycle these materials.
Building a new, circular value chain for plastics is a complex challenge that requires innovation at multiple levels — from developing new materials and recycling technologies to creating the infrastructure that will enable these materials to be collected and processed at scale. Through our work with partners like NREL, Glacier, and Novamont, we're demonstrating that this transformation is possible.
While there is still much work to be done, we are encouraged by the progress we've made with our partners. We are excited that by continuing to invest in research, support innovative startups, and collaborate across the value chain, we are at the forefront of a more sustainable future for plastics.